An Overview of the Working Principle, Advantages, and Application Fields
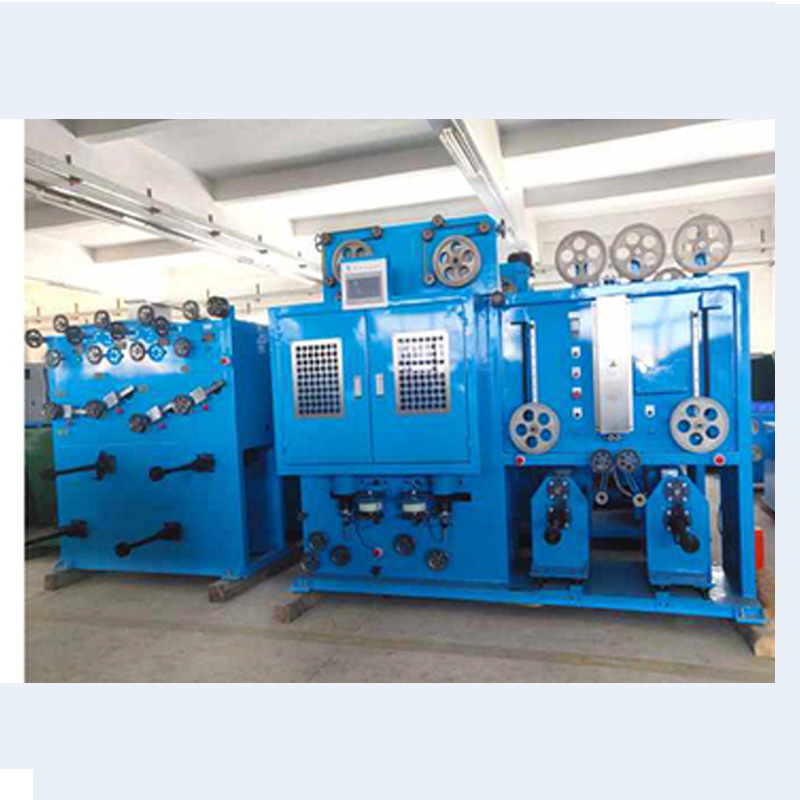
The twin-screw extruder is a remarkable piece of equipment that revolutionizes various industries by offering a highly efficient and versatile solution for material processing. Its unique engineering design and multiple advantages make it an indispensable tool in the manufacturing world. This article will delve into the working principle, advantages, and application fields of the twin-screw extruder.
Working Principle
The twin-screw extruder comprises two intermeshing screws that rotate in the same direction within a stationary barrel. These screws are precisely engineered with a specific profile to create a tight intermeshing configuration. As the material enters the feed section, it is conveyed through the barrel due to the screws' rotation. The screws' unique design allows for excellent mixing, shearing, and compressing of the material, resulting in efficient melting and homogenization.
The working principle of the twin-screw extruder can be further divided into various zones. The feed zone facilitates material feeding, the compression zone enables the removal of any trapped air or gases, the melting zone ensures the complete melt of the material, and the homogenization zone achieves the desired uniformity. The modular design of the twin-screw extruder allows for the incorporation of additional screws or barrels to enhance specific processing requirements.
Advantages
The twin-screw extruder offers numerous advantages over traditional single-screw extruders, making it a preferred choice in many applications. Firstly, its exceptional mixing capabilities ensure superior dispersion of additives, fillers, and reinforcing agents within the material. This results in improved product quality, consistency, and performance.
Secondly, the twin-screw extruder provides precise control over the processing parameters, such as temperature, pressure, and screw speed. This flexibility allows for efficient processing of a wide range of materials, including thermoplastics, thermosets, elastomers, and even food products.
Furthermore, the twin-screw extruder has a significantly higher throughput compared to single-screw counterparts. This, coupled with its ability to achieve a consistent and uniform melt, increases productivity while reducing manufacturing costs.
Application Fields
The versatility of the twin-screw extruder makes it applicable in a wide range of industries. It finds extensive use in the plastics industry for compounding, blending, and pelletizing operations. Additionally, it plays a crucial role in the food industry for creating various food products, such as pasta, snacks, and cereals.
Moreover, the twin-screw extruder is vital in the pharmaceutical industry for manufacturing drugs, where precise control over the mixing and granulation process is crucial. It also finds applications in the chemical industry for processes such as reactive extrusion and polymerization.
In summary, the twin-screw extruder is an engineering marvel that offers numerous advantages and finds applications in various industries. Its working principle, with intermeshing screws and precise control over processing parameters, ensures efficient material processing. The advantages it offers, such as excellent mixing, precise control, and high throughput, make it an indispensable tool. With its versatile applications in plastics, food, pharmaceutical, and chemical industries, the twin-screw extruder stands at the forefront of modern material processing technology.