A Comprehensive Study on the Process and Application of Sheet Extrusion
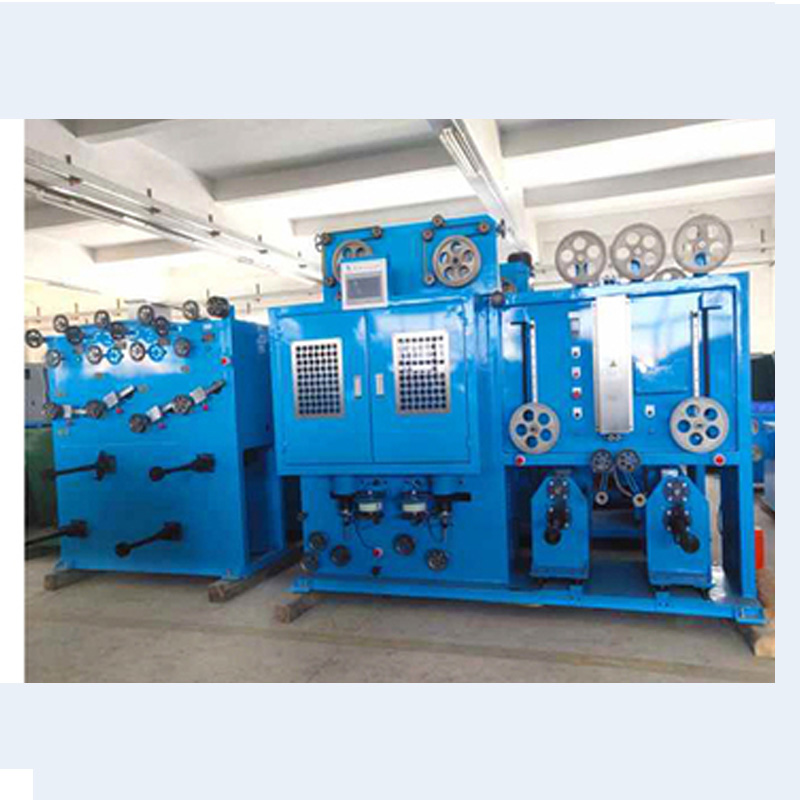
Sheet extrusion is a widely used manufacturing process in the plastic industry. It involves the formation of continuous plastic sheets by forcing molten plastic material through a die. This article aims to provide a detailed analysis of the sheet extrusion process, highlighting its various applications and case studies.
The Sheet Extrusion Process
The sheet extrusion process consists of several key stages:
1. Polymer Melting: The raw plastic material, typically in granule or pellet form, is melted using heat and pressure in an extruder machine.
2. Extrusion: The molten plastic is forced through a flat die, which determines the thickness and width of the sheet. The extruded sheet is then cooled down using a roller system or water cooling bath.
3. Hauling: The cooled sheet is pulled or hauled by rollers or belts to maintain the desired tension and speed.
4. Cutting and Winding: The sheet is trimmed to the required length and wound into large rolls for further processing or transportation.
The Applications of Sheet Extrusion
Sheet extrusion finds a wide range of applications in various industries:
1. Packaging: Sheet extrusion is used to produce plastic sheets for packaging applications such as thermoforming trays, blister packs, and food containers. These sheets provide excellent clarity, durability, and barrier properties.
2. Construction: Plastic sheets produced by extrusion are commonly used in the construction industry for applications such as roofing, wall cladding, and glazing. They offer lightweight, weather-resistant, and cost-effective alternatives to traditional materials.
3. Automotive: Sheet extrusion enables the production of plastic sheets used in automotive parts such as interior trim, door panels, and instrument panels. These sheets can be easily molded, painted, and shaped according to the desired design.
Application Case Analysis
Case 1: Packaging Industry - Thermoforming Trays
A food packaging company utilized sheet extrusion to produce thermoforming trays for perishable products. By using specialized plastic materials with excellent barrier properties, the company was able to extend the shelf life of the products while ensuring their safety and freshness during transportation.
Case 2: Construction Industry - Roofing Sheets
A construction company incorporated extruded plastic sheets as roofing materials in a commercial building project. The lightweight and durable nature of the sheets allowed for easy installation, reduced maintenance costs, and improved energy efficiency by providing better insulation.
Case 3: Automotive Industry - Interior Trim
An automotive manufacturer adopted sheet extrusion to produce plastic sheets for interior trim components. The versatility of the extrusion process enabled the company to create customized designs, colors, and textures, resulting in visually appealing and comfortable interiors for their vehicles.
Conclusion
The sheet extrusion process is a versatile and efficient method for producing plastic sheets with a wide range of applications. Its benefits include cost-effectiveness, customization options, and the ability to create products with desirable properties. Through various application case studies, it is evident that sheet extrusion plays a vital role in industries such as packaging, construction, and automotive.