An In-depth Discussion on the Challenges and Solutions
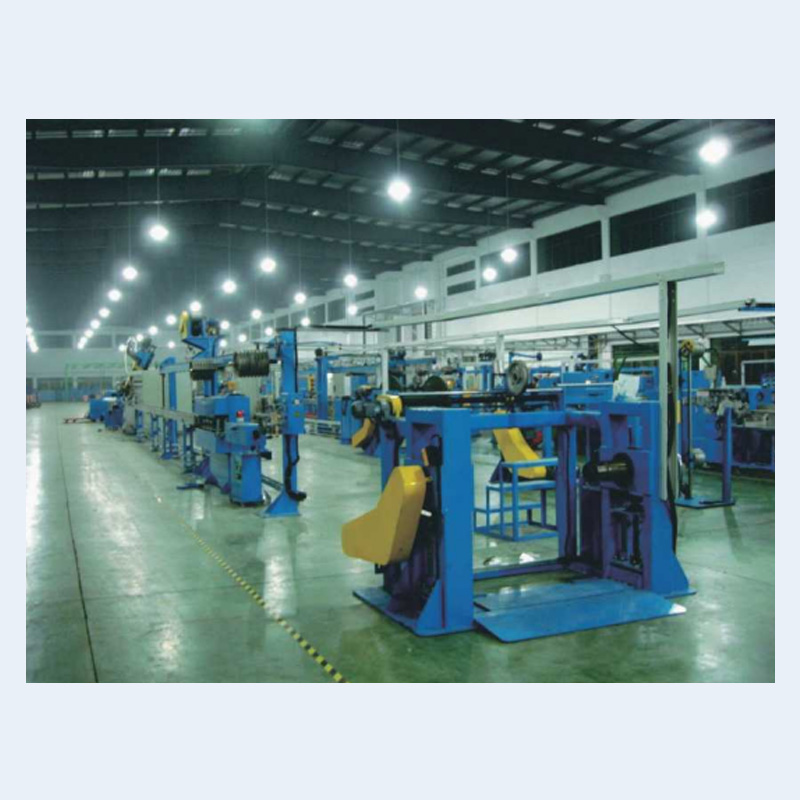
Silicone extrusion is a vital process in the manufacturing of various silicone products. However, it is not without its challenges. In this article, we will explore common problems faced during the silicone extrusion process and share effective solutions to overcome them.
1. Uneven Extrusion Output
One common issue faced during silicone extrusion is the uneven output of the material. This can result in products with inconsistent dimensions and surface quality. Several factors contribute to this problem, including:
- Inadequate die design or improper die alignment
- Insufficient cooling or curing time
- Uneven temperature distribution along the extruder
To address this issue, it is crucial to ensure proper die design and alignment. Regular maintenance and calibration of the extruder can help maintain consistent temperature distribution. Additionally, optimizing cooling and curing time based on the specific silicone formulation is essential for achieving uniform extrusion output.
2. Air Traps and Bubbles
Air traps and bubbles are another common problem faced during the silicone extrusion process. They can result in defects such as weak seals or reduced product durability. The following factors can contribute to the formation of air traps and bubbles:
- Inadequate degassing of raw materials
- Inefficient temperature regulation causing air entrapment
- Improper extruder setup leading to air pocket formation
To prevent air traps and bubbles, it is crucial to thoroughly degas the raw silicone material before extrusion. This can be achieved through vacuum degassing or utilizing appropriate additives. Maintaining consistent temperature control throughout the extrusion process is also essential. Proper setup and adjustment of the extruder and die can minimize the formation of air pockets and further reduce the occurrence of air-related defects.
3. Poor Adhesion and Bonding
Poor adhesion and bonding between silicone parts can pose a significant challenge in the silicone extrusion process. This can result in weak joints and compromised product integrity. Common factors contributing to poor adhesion and bonding include:
- Contamination on the surface of the silicone material
- Inadequate surface preparation
- Improper curing conditions
To achieve strong adhesion and bonding, it is essential to ensure a clean and contamination-free surface. Proper surface preparation techniques such as cleaning, degreasing, or plasma treatment should be employed. Additionally, choosing the appropriate adhesive or bonding agent and optimizing the curing conditions based on the silicone formulation can significantly improve bonding strength.
Conclusion
Successful silicone extrusion requires addressing common challenges and implementing effective solutions. By focusing on optimizing die design, maintaining proper temperature control, degassing raw materials, and ensuring adequate surface preparation and curing conditions, manufacturers can overcome the issues of uneven extrusion output, air traps, bubbles, and poor adhesion. By implementing these solutions, silicone extruders can achieve consistent, high-quality products, meeting the demands of diverse industries.