Introduction
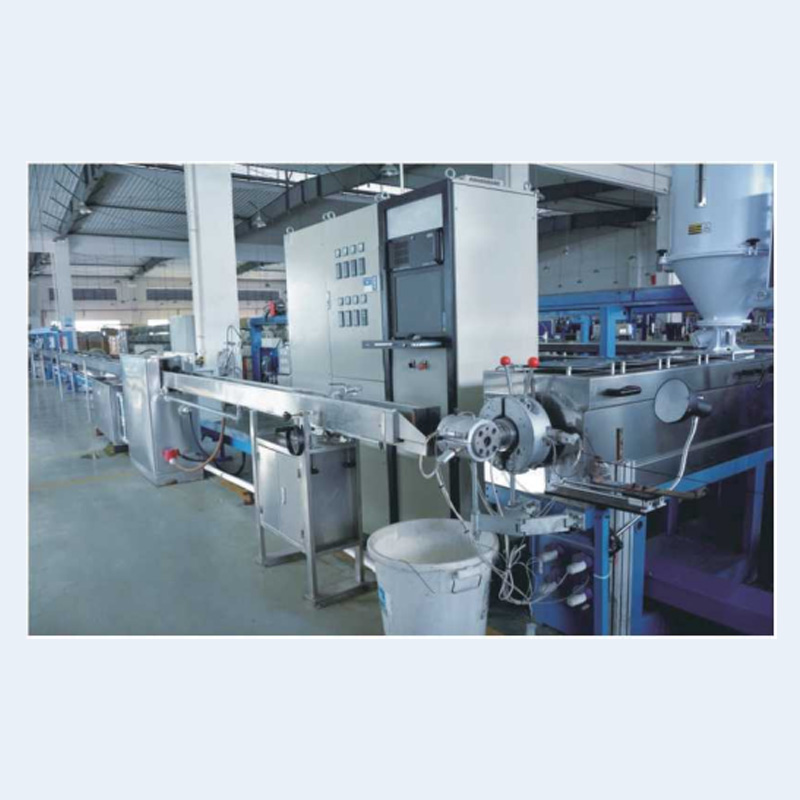
Plastic pipe extrusion is a common manufacturing process used in the production of plastic pipes. To ensure the quality of the extruded pipes, it is essential to study and optimize the process parameters and establish effective control methods. This article aims to explore the research conducted on the process parameters and product quality control methods in plastic pipe extrusion using pipe extruders.
Process Parameters
The process parameters in plastic pipe extrusion have a significant impact on the final product quality. These parameters include temperature, screw speed, melt pressure, cooling rate, and die design. The temperature of the extruder barrel and die influences the melt viscosity and thermal degradation of the plastic material. The screw speed affects the material mixing and melting efficiency. Melt pressure affects the wall thickness and overall integrity of the pipe, while the cooling rate determines the dimensional stability. The die design should be optimized to ensure uniform flow and minimize the occurrence of defects.
Product Quality Control Methods
To maintain consistent and high-quality production, various quality control methods are employed during plastic pipe extrusion. The following methods are commonly used:
1. Statistical Process Control (SPC)
SPC involves monitoring and controlling the process variables to ensure that the extrusion process is within acceptable limits. It includes the use of control charts to detect any variation in the process parameters, such as temperature, pressure, and product dimensions. By analyzing the control charts, deviations from the standard can be identified, and corrective actions can be taken to prevent quality issues.
2. Online Inspection Systems
Online inspection systems are used to monitor the product quality in real-time during the extrusion process. These systems utilize sensors and cameras to detect defects such as wall thickness variations, air bubbles, and surface imperfections. By identifying the defects early on, adjustments can be made to the process parameters to rectify the issues and ensure consistent product quality.
3. Non-Destructive Testing (NDT)
NDT methods are employed to evaluate the integrity and quality of the extruded pipes without causing any damage. Techniques such as ultrasonic testing, visual inspection, and pressure testing can be used to detect internal and external defects. NDT helps in identifying any flaws or weaknesses in the products, allowing for necessary corrective actions to be taken before the pipes are shipped to customers.
Conclusion
In summary, the process parameters and product quality control methods in plastic pipe extrusion using pipe extruders play a crucial role in ensuring the production of high-quality pipes. By optimizing the process parameters and implementing effective control methods like statistical process control, online inspection systems, and non-destructive testing, manufacturers can achieve consistent and reliable product quality. Continuous research and development in this field will further enhance the efficiency and quality of plastic pipe extrusion processes.