Exploring the Inner Workings of Screw Extruders
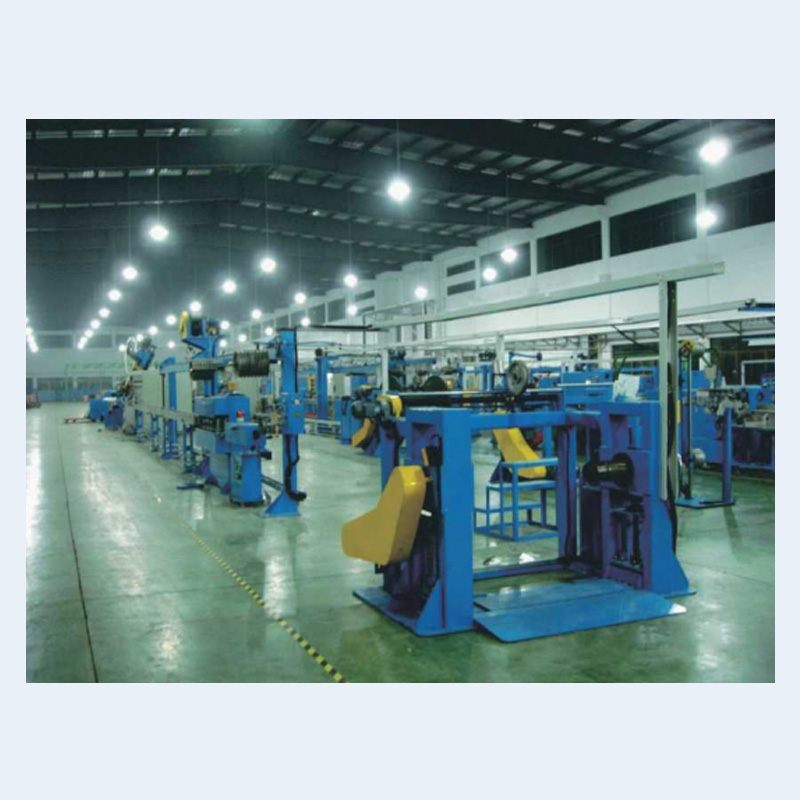
A screw extruder is a vital machine used in various industrial applications, including plastic manufacturing, food processing, and pharmaceutical production. In this article, we will delve into the design principle and precision control method of screw extruders, understanding the intricate details that make them efficient and reliable.
1. Screw Structure Design Principle
The performance of a screw extruder greatly depends on its design, specifically the structure of the screw. The following are the key design principles that ensure optimal operation:
a) Screw Diameter and Length: The diameter and length of the screw directly impact the output of the extruder. A longer screw allows for more contact time between the material and the barrel, resulting in better mixing and melting. A smaller diameter screw facilitates higher pressure build-up, ensuring efficient extrusion.
b) Flight Depth and Pitch: The flight depth and pitch dictate the conveying capacity of the extruder. A greater flight depth increases the material intake, while a larger pitch promotes material transportation and melting. These parameters should be carefully adjusted to achieve the desired extrusion rate and quality.
c) Screw Channel Design: The design of the screw channel can be either single-screw or multi-screw. Single-screw extruders are widely used due to their simplicity and versatility. Multi-screw extruders, such as twin-screw extruders, offer enhanced mixing capabilities and are suitable for complex materials.
2. Precision Control Method
Precision control is essential to maintain the quality and consistency of the extruded product. The following control methods ensure precise operation:
a) Temperature Control: Accurate temperature control along the barrel is crucial to achieve the desired material properties. The extruder employs heating and cooling systems to regulate the temperature of different sections. Thermocouples and PID controllers are frequently used for precise temperature monitoring and adjustment.
b) Screw Speed Control: The rotational speed of the screw determines the extrusion rate and residence time. By controlling the motor speed, the extrusion process can be fine-tuned to meet specific requirements. VFDs (Variable Frequency Drives) are commonly used to achieve precise screw speed control.
c) Pressure Control: Maintaining proper pressure is vital to prevent material leakage and achieve consistent product dimensions. Pressure sensors and control valves are employed to monitor and regulate the pressure within the extruder. This ensures stable extrusion and avoids product defects.
Conclusion
In summary, understanding the screw structure design principle and precision control method of screw extruders is crucial for optimizing their performance. By considering the screw diameter and length, flight depth and pitch, and screw channel design, engineers can design extruders suitable for specific applications. Additionally, precise temperature, screw speed, and pressure control guarantee the production of high-quality extruded products. Mastering these principles and control methods can significantly enhance operational efficiency and product consistency in various industries.